Hot Topics and Industry Discussions on Car Seat Static Strength Testers
Time:
Popularity:0times
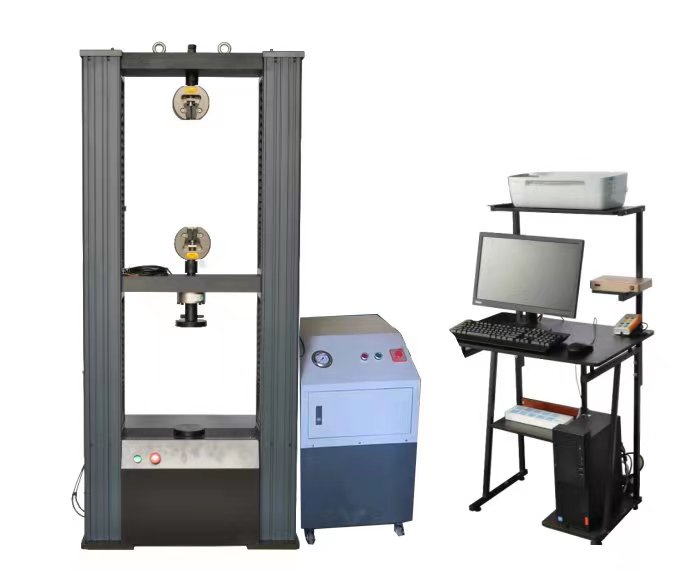
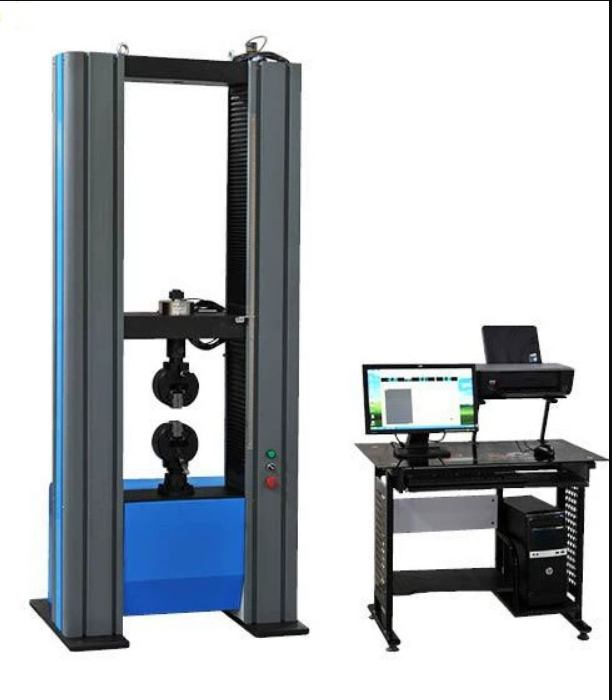
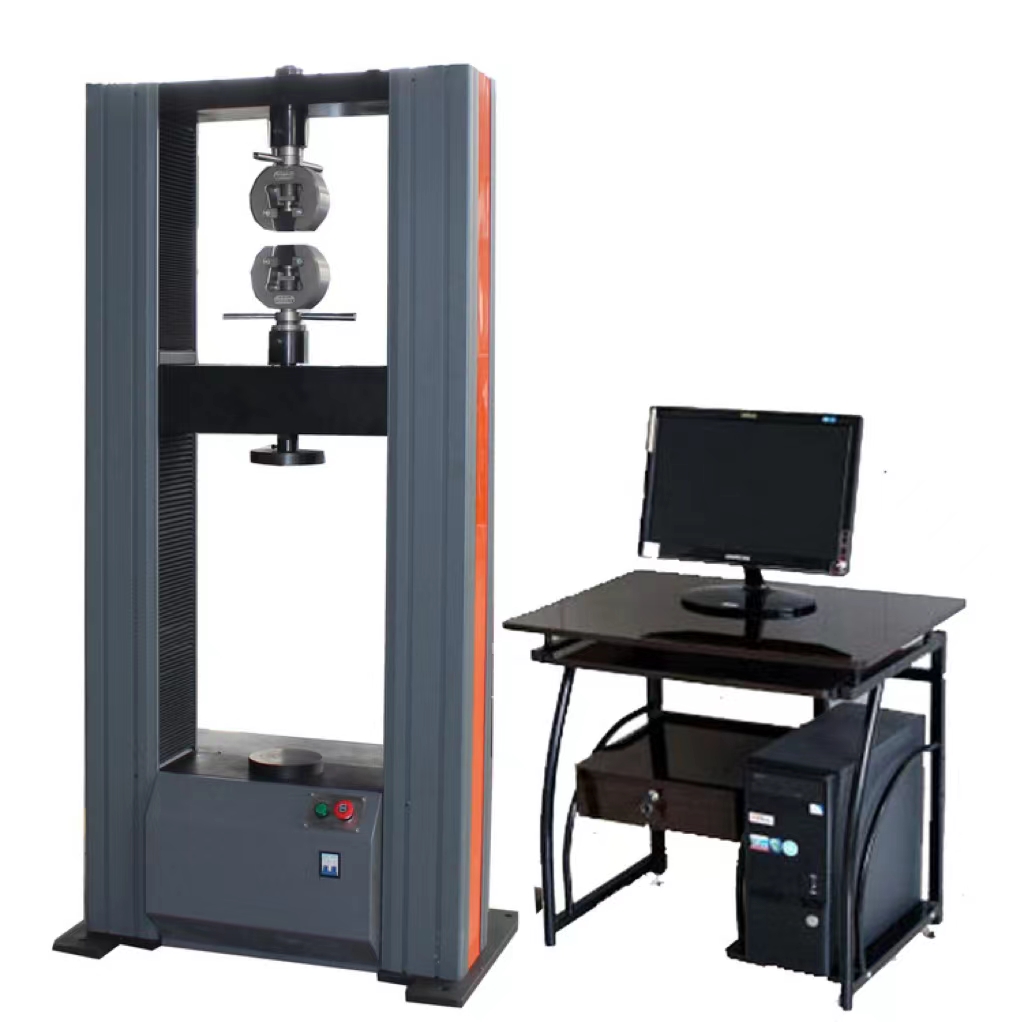
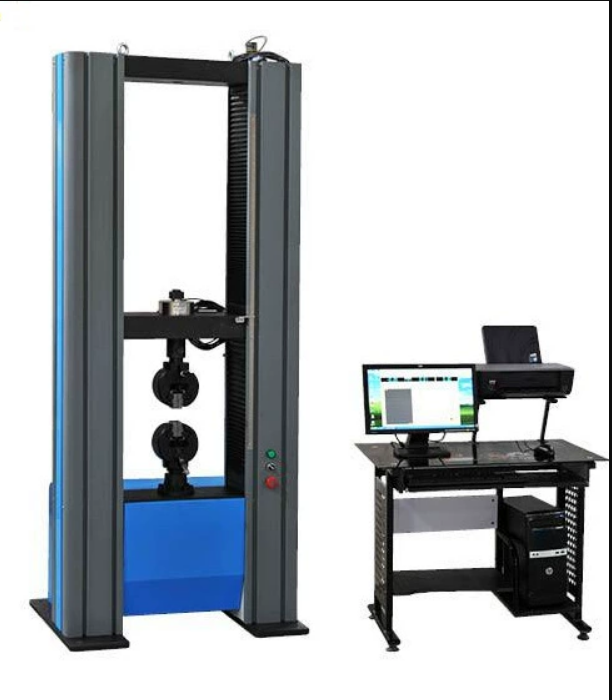
1. Global Regulatory Harmonization and Stringent Standards
- Evolving Regulations: Recent updates to ECE R17, FMVSS 207, and GB 15083-2019 have heightened scrutiny on seat strength and durability. For instance:
- The ECE R17 Amendment 8 (2023) introduced stricter criteria for seatback integrity under lateral loads, prompting manufacturers to redesign seat structures.
- FMVSS 207 now mandates testing under oblique loads to simulate real-world crash scenarios, requiring testers to adapt their methodologies.
- Industry Response: Manufacturers are investing in multi-axial testing rigs capable of applying combined vertical, horizontal, and torsional forces, ensuring compliance with diverse regulatory frameworks.
2. Advancements in Testing Technologies
- Digital Twin Integration: Automakers are leveraging digital twin simulations to predict seat behavior under static loads before physical testing. This reduces prototyping costs and accelerates certification processes.
- AI-Powered Analysis: Machine learning algorithms are being employed to analyze test data, identifying patterns that may indicate potential weaknesses in seat designs.
- Sustainability in Testing: There is a growing focus on eco-friendly materials and recyclability in seat construction, with testers evaluating the impact of these materials on structural integrity.
3. Challenges in Meeting Modern Safety Demands
- Balancing Weight and Strength: The shift toward lightweight materials (e.g., composites, aluminum) to improve fuel efficiency poses challenges in maintaining seat strength. Testers must ensure these materials meet safety standards without compromising performance.
- Electrification and Autonomous Driving: The rise of electric vehicles (EVs) and autonomous driving systems introduces new seating configurations (e.g., zero-gravity seats, rotating seats), requiring innovative testing protocols.
- Regional Disparities: While global standards like ISO 12092 exist, regional variations (e.g., CMVSS 210 in Canada) necessitate flexible testing strategies for multinational manufacturers.
4. Innovations in Seat Design and Testing
- Active Safety Features: Seats with integrated pretensioners, energy-absorbing foams, and headrests are becoming standard. Testers are developing new metrics to evaluate the effectiveness of these features under static loads.
- Virtual Testing Validation: Collaborations between regulatory bodies and manufacturers are driving the development of virtual certification processes, where physical tests are supplemented by simulations to streamline approvals.
- Post-Crash Occupant Dynamics: Recent studies on post-crash occupant kinematics highlight the need for testers to assess not only seat strength but also how seats interact with other safety systems (e.g., airbags, seatbelts).
5. Industry Collaboration and Future Outlook
- Cross-Sector Partnerships: Automotive OEMs, suppliers, and testing laboratories are forming alliances to share best practices and accelerate innovation in seat safety.
- Standardization Efforts: Organizations like ISO and ASTM are working to harmonize testing protocols, reducing redundancy and facilitating global trade.
- Long-Term Vision: The industry is exploring the integration of smart seats with health monitoring sensors, requiring testers to expand their scope beyond structural integrity to include biometric data analysis.